La valeur de la maintenance prédictive ne réside pas seulement dans le remplacement d'anciennes technologies par des nouvelles. Il s'agit avant tout de l'association solide d'algorithmes d'une part et de la symbiose homme-machine d'autre part pour hisser votre maintenance à un niveau supérieur.
Algorithmes et processus
La deuxième révolution industrielle, qui a principalement eu lieu en Amérique et qui portait sur le remplacement des machines à vapeur par l'électricité, n'a généré aucun gain de productivité au cours des premières décennies. L'ancienne technologie (machines à vapeur) a tout simplement été remplacée par une nouvelle (électricité). Ce n'est qu'avec l'arrivée d'une nouvelle génération de managers que la productivité a été stimulée, car ils ont utilisé la flexibilité de la nouvelle technologie et ont adapté les processus en fonction de celle-ci. Cette condition s'applique également à la maintenance prédictive : sa valeur économique réelle ne sera débloquée que si des ajustements structurels du processus sont également mis en œuvre.
Un exemple concret d'un tel ajustement du processus est le passage d'un flux poussé à un flux tiré. Cette transition améliore considérablement l'efficacité et l'efficience de la maintenance. Traditionnellement, la maintenance est organisée selon un flux poussé. Sur la base des données du fournisseur, un schéma de maintenance est établi et exécuté à une fréquence fixe. Ces schémas sont basés sur une approche pessimiste, prenant en compte les moins performants du groupe, un dénominateur commun principal et donc pas l'état d'une machine individuelle. Lorsque nous donnons un aperçu de l'état actuel et faisons des prédictions sur l'état futur d'une machine, nous pouvons également passer à un flux tiré pour les activités de maintenance. Le flux tiré est basé sur la demande du « client » et ne produit que ce qui est demandé. L'état futur d'une machine déclenchera alors des activités de maintenance, créant ainsi une demande de maintenance. La demande est initiée par un algorithme de maintenance prédictive, mais ce n'est qu'en combinaison avec l'expertise de l'ingénieur que la demande de maintenance sera effective.
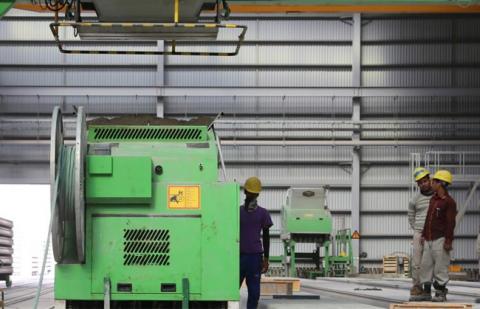
Symbiose homme-machine
Une machine n'est pas devenue une base de données et les données ne sont pas sacrosaintes. Une machine reste principalement mécanique. Par conséquent, l'association des connaissances fondées sur les données et l'expertise de l'ingénieur représente la deuxième clé de la valeur économique réelle. Une machine que l'on transforme pour fabriquer de nouvelles pièces produit de « nouvelles » données et les algorithmes devront s'adapter en conséquence. Dans une première phase, la marge d'erreur d'une telle machine est plus grande et il convient d'en tenir compte au cours de l'interprétation. En outre, il va de soi que des situations qui ne se sont pas encore produites ne peuvent pas être prévues sur la base des données historiques.
Les données historiques en elles-mêmes fournissent un « paradoxe de maintenance prédictive ». La maintenance préventive qui est effectuée permet d'éviter autant que possible les activités de maintenance corrective. Cela implique que les données historiques ne contiennent que les problèmes qui ne pouvaient pas être évités par les activités de maintenance préventive, les exceptions. Cette opération fournit aux entreprises des données très biaisées, des données qui ne sont pas adaptées au développement de la maintenance prédictive. Par ailleurs, les entreprises ne disposent souvent que d'un nombre limité de données historiques, voire d'aucune donnée. Dans ces cas, des algorithmes d'apprentissage non supervisé offrent une solution.
Les algorithmes d'apprentissage non supervisés ne s'appuient pas sur des données étiquetées, mais forment des modèles utilisant des données de base pour définir le comportement normal de la machine. Les nouvelles données des capteurs sont évaluées par rapport à ces données de base, qui caractérisent un comportement et indiquent tout écart par rapport au comportement normal. La vibration est une valeur de capteur efficace courante et éprouvée. En mesurant les vibrations d'un composant d'une machine, le comportement anormal peut être déterminé de manière très précise et automatique. Il reste toutefois du chemin à parcourir avant d'y arriver, car les vibrations sont le symptôme d'un problème sous-jacent. Cette difficulté nous renvoie au technicien de maintenance qui doit déterminer la cause réelle en se basant sur les symptômes. Le technicien qui examine les différences dans les valeurs des capteurs telles que les vibrations, la consommation électrique, la température ou la pression, sera en mesure d'effectuer une analyse approfondie et de demander un intervalle de maintenance plus précis. Une application parfaite du flux tiré.
En surveillant activement les valeurs des capteurs de la machine, nous pouvons évaluer l'impact des activités de maintenance. La machine revient-elle en arrière en fonction de la ligne de base après la maintenance ou constate-t-on encore un comportement anormal et y a-t-il encore un risque de panne possible ? L'évaluation continue des activités de maintenance permet également d'y apporter des améliorations.
Un impact positif dans de nombreux domaines
Le passage d'un flux poussé à un flux tiré pour la maintenance se fait de manière très progressive. Les intervalles de maintenance sont progressivement reculés en fonction des prévisions qui sont renforcées par les connaissances et l'expérience des collaborateurs. Petit à petit, la fréquence des maintenances est réduite à un point optimal et les coûts sont réduits. La valeur économique ne se limite pas seulement à la réduction des coûts de maintenance : elle a également un impact positif sur la qualité, la sécurité, la durée de vie et la disponibilité des machines. Ce dernier point, la disponibilité, a un lien direct avec le chiffre d'affaires. Chaque amélioration de la disponibilité se traduit par une augmentation de la production, ce qui illustre la valeur économique élevée de la maintenance prédictive. La maintenance prédictive ne fait pas que modifier les intervalles de maintenance au fil du temps. Elle fait également progresser les activités de maintenance pour éviter les arrêts si nécessaire. Une étude de PwC montre une amélioration moyenne de la disponibilité de 9 % en cas de transition vers la maintenance prédictive. Vous pouvez déjà commencer à calculer.